Eddy Current Drives: First Choice for High Performance and Reliable Operation
You have several choices when it comes to drive technologies. But when the cost of downtime enters the decision making, the field narrows… to eddy current. Why? Because no other drive system operates with such simplicity, with so few parts to wear out, and with so little maintenance. Once you pencil in the total cost of downtime for your process, the lost material, the lost labor, the lost output, you’ll see why many system designers and engineers specify high performance eddy current drives.
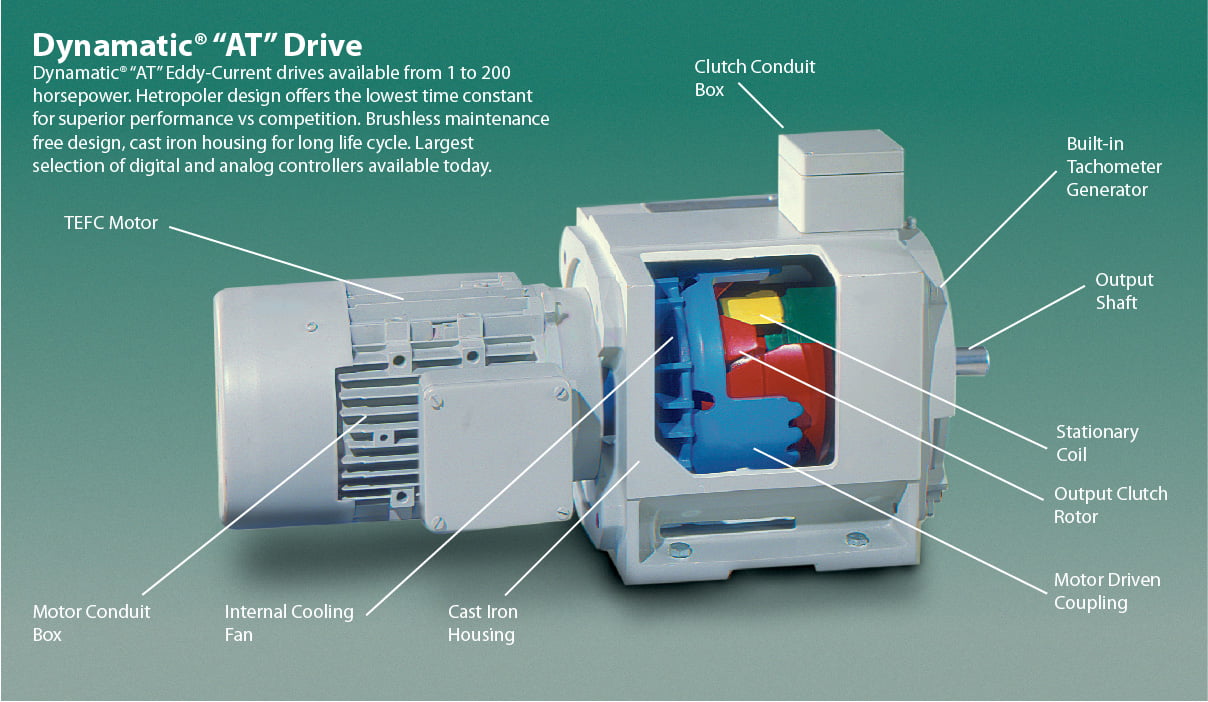
Simplicity makes the difference.
A typical eddy-current drive consists of a NEMA design B induction motor, eddy-current magnetic clutch and a compact solid-state controller. The motor powers the clutch directly, with the controller handling only 1 percent of the power.
Dynamatic eddy current drives contain only two motor bearings and two clutch bearings. Since torque is transmitted through an electromagnetic coupling there is no wear as occurs with drives which utilize friction material or belts to transmit torque. No slip rings or brushes to replace or clean, just four bearings ensure more uptime, and minimal maintenance… all of which are advantages manufacturers find especially important. Additionally, the TEFC motor allows for outdoor operation. A cast iron housing, brushless clutch coil, and solid-state controllers, are ideal features for harsh conditions – oil, dirt, dust, high humidity and more! And since eddy current drives are cooled internally by ambient air, you don’t need complicated cooling systems that often fail.
Simplicity also means low maintenance cost.
No adjustable speed system is easier to maintain than an eddy current drive. With so few parts to wear and a simple design for quick troubleshooting, they add savings to the bottom-line year after year.
The circuitry in Dynamatic controllers is compact, straightforward and interchangeable among a wide range of drive horsepowers. So, modifications are not complicated, and inventory is minimal.
Since there are no fast switching devices, the controllers meet FCC Part 15, Class A and B. They also meet the requirements of ANSI/IEEE 519 without the use of line fillers, capacitors and chokes.
Easy to install
To begin with, eddy current drives are among the least expensive adjustable speed drives. And since they run on three-phase voltage input, they can operate on existing wiring and power sources to save installation costs and to make easy retrofitting.
Eddy current drives are ideal for machines exported around the world. Models are available that run on either 50 or 60 cycle power. And they don’t require highly trained personnel to install. In fact, they are as easy to install as electric motors.
You can install eddy current drives in hard to get at places, such as towers, pits, or on top of large machines, because the controllers can be up to 500 feet away. And you can use eddy current drives for vertical applications without expensive modifications.
Eddy Current Drives perform the way you want
Eddy current drives offer superior speed control for smooth operation and prevention of breakage. For instance, eddy current drives with tachometer generator feedback let you maintain speed within ½% for load changes all the way from no load to full load.
You get a full 34 to 1 speed range at rated torque in eddy current drives up to 200 horsepower. In fact, they produce up to 250 percent of rated motor torque for starting and momentary conditions. No other system can match this performance.
Improves productivity
High torque along with stepless speed control has allowed a number of industries to improve productivity and produce higher quality products. A wide range of pre-engineered controller options are available. You’ll find then used for material handling, load-share conveyors, machine tools, paper winding, batch handling, wastewater treatment, pumping, packaging… anywhere speed changes, including starting and stopping, must be smooth and controlled.